Improving Sustainability with QCS Lifecycle Management
Since their inception, Quality Control Systems (QCS) have played an integral role in the quality and efficiency of the paper industry. There are occasions when it is time to upgrade to the latest version of QCS due to obsolescence or cost effective technological advances. However; in these days of being asked to do more with less, there are incidents when the capital dollars needed to upgrade are just not available.
Agility is required in these circumstances to sustain the life of the QCS while maintaining or improving profitability. In recent years forward thinking QCS engineers have found many of the answers in system virtualization, recycled or repaired parts, alternative parts solutions, being better prepared for the corrective maintenance evolutions, and improved preventative maintenance programs to improve the QCS life cycle and prolong the need for capital.
INTRODUCTION
Pulp and Paper Professionals have long recognized the contributions that the Quality Control System (QCS) provides the industry. Because the QCS is responsible for measuring, reporting, and controlling the variability in the machine direction (MD) and the cross machine direction (CD), they are also well aware of the impact felt when the equipment fails to perform.
Even though there have been technological advancements by the QCS suppliers, many paper companies evaluate the business and financial reasons and deem it unnecessary to upgrade. Through the years QCS suppliers have released numerous generations of Quality Control Systems that are still in existence today. Some of them go as far back as the 1980’s. In any case, the personnel responsible for the maintenance and performance of the QCS equipment have been tasked to seek better performance and extend the life of the legacy systems.
CHALLENGES
There are challenges to be dealt with when a mill decides to preserve a legacy QCS; however, not identifying the hurdles and having processes in place to address them will expose a company to risks. Listed below are a few of the more common hurdles that paper mills and their QCS personnel have encountered through the years.
• Parts obsolescence. With the shorter life cycle of PC/server technology, this is becoming even more of a challenge.
• Communication difficulties with newer data historian and other process control equipment such as DCS and PLC.
• Age of equipment.
• Lack of technical support. Once a particular product has entered the end of life phase and is considered no longer supported, it can be difficult to find senior level support.
SOLUTIONS
1. QCS maintenance personnel have discovered several unconventional methods to address parts obsolescence.
a. In order to replenish legacy parts at a significant savings, sources in both circuit board repair centers and recycled parts suppliers are being used on a routine basis. Some of these pioneering engineers have even leveraged their technical know-how to find cases where parts substitution is feasible. For example there are methods for replacing tape and hard drives with solid state devices. Another example is replacing a cross directional control cabinet obsolete PLC with a desktop and an off-the-shelf data acquisition device.
b. Since PC technology changes faster than most QCS systems upgrade, virtualization is a proven method for addressing obsolescence and extending the life cycle of PC/server based systems in many cases. The principal idea behind hardware virtualization is not complex. To create a virtual machine (VM), the physical computer is being emulated using software. To take it a step further, several operating systems are capable of running on a single physical machine by using multiple VMs at once.
2. As mills upgrade to data historians and other process control equipment, they are learning to leverage other technological advances to add communication interfaces. Many of the legacy systems are not compliant with communication protocols, such as OPC. This makes communication difficult when mills have upgraded other technical equipment; however, there are several companies available that specialize in creating inexpensive and proven interfaces that will solve issues communicating with data historians and other process control equipment problem for the legacy QCS. This allows legacy system data to be used in new ways.
3. When you think about the age of the equipment, right away you must acknowledge how important it is to be in a more predictive maintenance mode instead of preventative maintenance. Knowing that it is impossible to stop every failure and how important it is to minimize downtime, you must also acknowledge how important it is to be better prepared for the corrective maintenance evolutions. As always one of the first steps is analyze the spare parts inventory and identify the vulnerability. As always, better historical sensor documentation leads to earlier recognition when trouble is on the horizon. It is also important that the maintenance personnel be familiar with the built in diagnostics and maintenance programs available. New diagnostic capabilities are being developed by field engineers to better predict the maintenance that is needed even on legacy systems.
4. In order to address the lack of technical support, it is incumbent upon the mill to ensure that the personnel servicing their legacy QCS be invested in so they have the skills necessary to maintain and optimize the aging equipment. In order to make-up for the lack of technical support it is imperative that the service personnel have access to subject matter experts that are still available. Allowing remote monitoring from senior level process control experts is a means to obtain extra support if needed.
CONCLUSIONS
By removing the perceived obstacles and being willing to try effective solutions many mills are not only extending the life of their QCS, but also lowering the total cost of ownership, thus allowing mills to spend the savings on other critical components to quality and production.
References
Chappell, David. "Virtualization for Windows: A Technology Overview" San Francisco. 2008. Web. 17 Jan. 2014
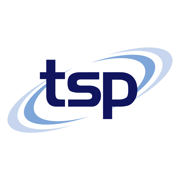
Related news
Do's and Don'ts of a Good Interview — For the Interviewer
One of the most important steps in hiring an employee is having the ability to conduct quality...
3 Reasons to Outsource Staffing
Business outsourcing is a key ingredient for many businesses success. Bringing in outside help for...
3 Reasons Why Companies Fire Their IT Service Providers
This post originally appeared onIT Briefcase.
Retention is often talked about among IT...