OEM Meaning, Examples, and Benefits
The right equipment and technology are critical to keeping your business running efficiently. With so much of the world reliant on digital infrastructure, you want to be able to get the tools you need and make the most of them. You may have seen advice to take advantage of OEM equipment when buying for your company. To do that, you need to understand OEM's meaning and how to make the system work for you.
OEM MEANING EXPLAINED
“OEM” stands for "Original Equipment Manufacturer.” The definition of an OEM is a company that designs and manufactures components or products that are used in the assembly of another company's final product.
In the context of IT, an OEM is often the supplier of hardware components (like motherboards, processors, or storage devices) or complete devices (such as laptops or printers) that are rebranded and sold by other companies. Many IT products you use may contain parts or technology from multiple OEMs.
An OEM will often bundle all the components into the configurations you need. They can also sell you parts in the quantities you want for your specific purposes. This creates convenience and flexibility for your team since you can control how much work must happen onsite. Working with an OEM or a company that has relationships with OEMs, such as TSP, can go a long way in simplifying how your business addresses technological needs.
DOES OEM MEAN THE SAME THING AS ORIGINAL EQUIPMENT?
While the term "OEM" refers to the original manufacturer of a product or component, it does not always mean you’ll get the exact same product you might find under the brand name of the company selling the final product. OEM products are often made to the same specifications as those found in the branded version but may differ in certain aspects, such as packaging, labeling, or warranty terms.
OEM MEANING VS. AFTERMARKET MEANING
To fully understand OEM’s meaning, it's also important to acknowledge aftermarket manufacturing and services. This is the opposite of OEM, where instead of having the original manufacturer of a component continue the relationship to maintain and replace important parts, a third-party manufacturer can offer something that seems comparable.
In general, there are several risks with aftermarket manufacturing that you don't need to worry about when relying on an OEM. A major concern is quality. Most OEMs are well-known in their field and have a reputation to uphold, so they do everything they can to ensure their name is only attached to quality products. This includes sourcing quality materials and creating a careful manufacturing process.
Aftermarket manufacturers are usually less well-known and don't have the same kind of reputation management pressures to assure higher performance. These companies also may not have the same resources and access to suppliers. While many aftermarket IT components are perfectly serviceable, you don't have the same quality guarantees.
3 EXAMPLES OF OEMS IN BUSINESSES
To further explain OEM’s meaning in business, consider these well-known examples:
1. OEMs in the Automotive Industry
Companies like Bosch and Magna International supply parts like brake systems, steering components, and engine control units to major car manufacturers such as Ford, Toyota, and Volkswagen.
2. OEMs in Computer Hardware
Companies like Seagate and Western Digital are OEMs that produce hard drives, SSDs, and other storage devices. These components are sold under the names of larger computer manufacturers or used in server systems. Similarly, NVIDIA and AMD provide graphics processing units (GPUs) that are used in everything from gaming computers to servers.
3. OEMs in the Aerospace Industry
Companies like Honeywell and General Electric supply parts such as engines, avionics, and flight control systems to major aircraft manufacturers like Boeing and Airbus.
IS IT OKAY TO BUY OEM PRODUCTS?
Yes, it is generally OK to buy OEM products, but it depends on your needs and expectations. They’re commonly used by businesses and manufacturers who need reliable components to build or assemble their own products.
OEM Benefits
To decide what working with an OEM might mean for your business, you need to consider the potential benefits. Embracing these opportunities could help put your company in a position to grow and expand in the future.
Cost savings
Almost by definition, OEM’s meaning is often associated with cost savings. It’s true: OEMs can save you money because most OEMs sell directly to other businesses. A business-to-business sales model is usually less costly to support, meaning the OEM doesn't have to pass extra costs along to you. You can also spend money on just the components or bundles you need, avoiding extra expenses that come with other tech solutions.
Time savings
It can be hard to track down all the components you need from various sources, whether you are trying to build new equipment or maintain your existing tools. An OEM can explain exactly what's available for you so your IT team doesn't spend a ton of time sourcing materials.
Support
You can also look forward to thorough support when you deal with an OEM. These companies want to be known as sellers of high-quality, long-lasting equipment that performs reliably. To ensure this, they generally put a lot of effort into support. With an OEM, you know exactly who to turn to for repairs or even replacements.
WHAT OEM MEANS FOR YOUR BUSINESS
As you focus on growing your company and improving operations, you don't want to have to worry about whether your team has access to the right parts and equipment. You want the assurance that everyone will have reliable tools to turn to in every scenario.
Once you understand OEM’s meaning, it's easy to see how using these companies for your IT equipment and support needs makes more sense. You can save money and time and improve reliability for all your systems.
However, deciding if an OEM is the right choice for your business involves weighing a few key factors:
- Cost vs. Benefit: While OEM products tend to be less expensive, it’s important to assess whether the savings are worth it. Consider the potential long-term benefits, such as increased reliability and reduced repair costs.
- Compatibility and Reliability: If you are working with specialized equipment or highly specific requirements, it’s essential to ensure that the OEM parts meet your needs and function seamlessly within your existing setup.
LET TSP WORRY ABOUT WHAT OEM MEANS
You can gain this confidence in your equipment by understanding OEM’s meaning and how it compares to other options. Or, better yet, partner with an IT service provider that can take care of the whole thing for you. If you are still trying to figure out the best way to create or navigate an OEM relationship, let TSP help. We have an extensive inventory of parts from top OEMs.
Our team can help you decide what you need and get it to your staff in a timely fashion. We can also assess your company's systems and show you how to get the most support from OEMs to keep your legacy systems going. Reach out today to get the IT maintenance solutions you need.
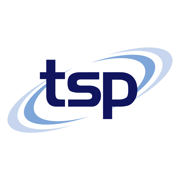
Related news
The Workaholics Guide to Relaxing on Vacation
Are you so used to over-functioning in your daily life that it seems impossible to find time for...
Debunking 3 Myths about OEM vs. Third-Party IT Support
Due to the many myths surrounding Original Equipment Manufacturer (OEM) and Third-Party...
3 Signs Your Business is Ready for Enterprise IT Support
When we talk to small to medium-sized business owners, they’re often surprised when we tell them...