What Is the Equipment Life Cycle?
Unlike heavy construction machinery and its multi-decade lifespan, IT equipment tends to live fast and burn out young. In the case of a well-known cloud service provider, the company has to replace one hard drive every two hours or so. Before planning for in-house and third-party infrastructure, every business needs to understand the equipment life cycle and related costs.
WHAT IS THE EQUIPMENT LIFE CYCLE IN IT?
The equipment life cycle refers to the journey that hardware goes through in your organization. Just like people progress from birth to retirement, tech devices also experience a series of phases from conception to replacement. For information technology and networking, there are eight main stages in the hardware life cycle.
1. System Design
Expert system design can be the difference between wasting funds and building a streamlined network that fits your company’s needs like a glove. This phase involves:
- Analyzing your organization’s technology needs
- Consulting with stakeholders and users
- Weighing in-house and third-party solutions
- Performing a use case assessment
- Considering factors such as cybersecurity compliance, budget, and personnel capabilities
2. Planning
The planning phase in equipment life cycle management includes fleshing out a purchase proposal. During this process, you need to analyze questions such as:
- What performance requirements does the system need to meet?
- What is the maximum budget for this purchase or project?
- How will staff use the equipment in regular operations?
- What is the purpose of purchasing this item, or what problem does it need to solve?
- How long should the equipment last with proper care and management?
- What is the average fail rate for this type of hardware in the industry?
Answering these questions is key to making smart decisions in the purchasing and procurement phases. For example, by looking at the equipment’s mean time to failure and annual failure rate, you can calculate your organization’s hardware needs for bulk orders and maximum purchase savings.
3. Purchasing/Procurement
Once you have a clear set of specs, it’s time to shop around for the best fit. Price is a large factor, but tech-savvy organizations know that quality and long-term performance often deliver lower operating costs overall, especially when you factor in downtime.
The procurement team researches multiple brands and vendors, considers pricing, and compares competing options. Instead of taking OEM claims at face value, look at real-world data on equipment performance, failure rates, and potential issues from professionals in the same industry.
Don’t be surprised if there’s some push and pull between IT and company executives. One group focuses on the bottom line and the other wants to ensure 24/7 uptime and top system performance.
4. Logistics and Deployment
Once you buy equipment, you still need to consider the cost of getting it ready for use:
- Logistics (especially for specialized or overseas hardware)
- Transportation and delivery
- Unloading and installation
- Equipment configuration
- User setup and onboarding
- Employee training
Don’t forget to factor in these steps when you run a cost-benefit analysis for accurate numbers.
5. Equipment Use/Operation
This phase covers the day-to-day usage of hardware, technology, or computer systems. All IT equipment has an MTTF that determines its average operational lifespan.
Equipment life cycle management includes ongoing performance monitoring, asset tracking, and condition evaluations. One reason is to ensure your workers utilize the equipment correctly and avoid damaging it.
To calculate the life cycle cost of equipment usage, don’t forget the need for regular updates, such as software and firmware security patches. In server rooms and data centers, air quality and climate control costs are other factors for long-term equipment operation.
6. Optimization
Testing and monitoring play a role in many stages of the equipment life cycle for IT, but they’re especially important when optimizing new equipment. Optimization means helping your company squeeze the most value out of equipment purchases.
Sometimes, this involves tweaking the configuration or adding performance-boosting accessories. Other times, it means showing your employees how to use little-known settings to simplify their work and increase efficiency.
7. Maintenance
Maintenance is critical for equipment in every industry. With a detailed program of system inspection, preventative maintenance, minor repairs, and timely replacement of worn parts, hardware can last many more years. IT systems also need regular cleaning to eliminate dust and prevent corrosion.
8. Disposal and Replacement
You never want equipment failure to catch your team by surprise. Good equipment life cycle management policies should gradually phase out hardware as it nears the end of its operational life, replacing it to ensure continual uptime.
In many industries, there are regulatory compliance factors to consider when decommissioning data storage hardware that contains sensitive information. You also need to factor in disposal costs and any relevant laws.
HOW DO YOU CALCULATE THE LIFE CYCLE COST OF EQUIPMENT?
To calculate equipment life cycle cost, add up all of the following expenses:
- Purchase price
- Labor costs for installation, upkeep, and upgrades
- Costs of maintenance, repair parts, and consumables
- Energy costs for use
Finally, subtract any salvage or resale value for equipment at the end of its life.
For networking hardware, always speak with your tax or accounting team to determine the correct depreciation schedule to zero. Tax laws generally set a limit for the depreciation of IT equipment like servers, computers, and similar equipment.
WHY IS EQUIPMENT LIFE CYCLE MANAGEMENT IMPORTANT FOR YOUR ORGANIZATION?
Understanding the life cycle of your company’s IT equipment helps you make cost-effective decisions. For example, if a major piece of hardware breaks down, weighing its current depreciation value against the cost of repair parts can help you decide whether repairs or replacement is the better option.
A maintenance program customized to your company’s needs can deliver increased equipment performance, uptime, and longevity. Put simply, you save money in the long run and avoid problems in the present.
EXPERTS IN EQUIPMENT LIFE CYCLE MANAGEMENT
IT experts can help with every stage of equipment life cycle management. At TSP, we can help your company find the right solutions for equipment, operating specs, installation, maintenance, and replacement cycles. Discover cost-effective, high-quality IT solutions today.
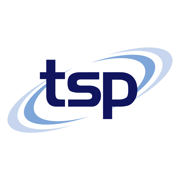
Related news
The One Thing That Can Speed Up Your IT Recruitment Process
The decision to hire a new employee isn’t one to take lightly. The average length of the hiring...
How to Ask if a Position Has Been Filled
Job hunting can be a chore under the best of circumstances, and uncertainty around role vacancies...
How to Impress Your Boss at Work
A strong relationship between you and your boss has the ability to transform your work experience....